Most requests are for upsizing a system that is already in use.
In the case of TOYO Engineering, however, the client built a new system in-house using Access, upsized it, and then put it into operation, making it a notable case study.
This is a notable method of one of the methodologies of EUC (end-user computing), and reasons for its success is the relatively easy upsizing made possible by AZD.
While ordering system development from scratch would have been extremely expensive, AZD made it possible to realize the client's request to create a system that could be used commonly at all locations around the world, while keeping costs down.
In the case of TOYO Engineering, however, the client built a new system in-house using Access, upsized it, and then put it into operation, making it a notable case study.
This is a notable method of one of the methodologies of EUC (end-user computing), and reasons for its success is the relatively easy upsizing made possible by AZD.
While ordering system development from scratch would have been extremely expensive, AZD made it possible to realize the client's request to create a system that could be used commonly at all locations around the world, while keeping costs down.
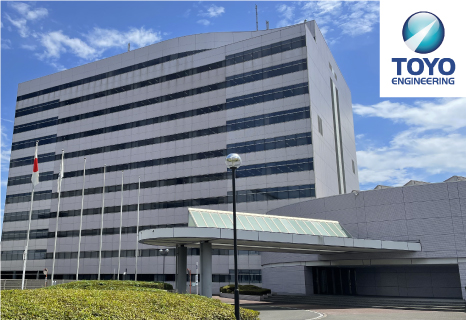
We want to build a database that allows centralized management of design data together with overseas locations.
TOYO Engineering are a specialized engineering company that operates a comprehensive engineering business. We mainly deal with hydrocarbon process plants and industrial infrastructure facilities, and provide engineering services such as design, procurement, and construction to domestic and overseas customers.
We have offices in various countries, and we provide engineering services efficiently to many customers by making full use of global operations with our offices when executing projects.
The Electrical Design Department, to which we belong, is in charge of designing electrical equipment for plants, but the design data handled for each project was actually managed individually by engineers at each site, mainly using Excel. With the increasing number of requests for digitalization from our clients, we were considering building a system that would enable us to centrally manage project data using a common design platform shared with our brunches in each country, based on our sense of urgency that the individual Excel management we had been using was not sufficient in terms of both speed and quality.
We have offices in various countries, and we provide engineering services efficiently to many customers by making full use of global operations with our offices when executing projects.
The Electrical Design Department, to which we belong, is in charge of designing electrical equipment for plants, but the design data handled for each project was actually managed individually by engineers at each site, mainly using Excel. With the increasing number of requests for digitalization from our clients, we were considering building a system that would enable us to centrally manage project data using a common design platform shared with our brunches in each country, based on our sense of urgency that the individual Excel management we had been using was not sufficient in terms of both speed and quality.
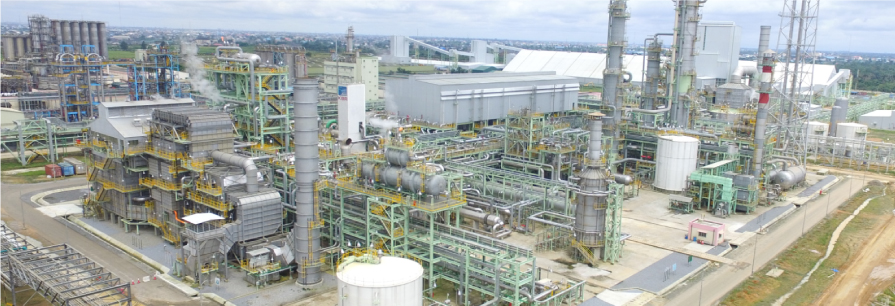
Visualize their needs with Access prototypes
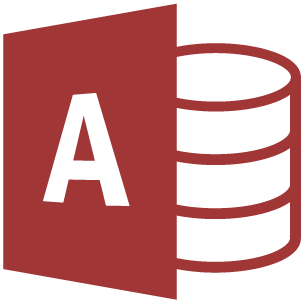
In our DX efforts, we were faced with the challenge of building a database-type tool for more advanced use of design and project data. We knew that the commercially available design tools could not meet our needs due to limitations in the data and functions they could handle. At first, we considered customizing a commercially available tool, but decided against it because the cooperation of the developer was required, development costs were expected to be high, and it was unclear whether our requirements could be reflected 100% due to the limitations of the software.
Next, we turned to in-house development and started with the definition of requirements. Based on the requirements definition, we tried to order a system vendor to create a program for us. The tool we were aiming for needed to incorporate the structure of electrical design and project execution that we had developed. There was a lot of tacit knowledge, and it was difficult to review and finalize the specifications. We were also concerned that the system vendor, who had no design knowledge, would not be able to accurately understand our intentions based on the requirements definition we had prepared. We decided to use a stand-alone design tool that we had created in Access about 20 years ago as a basis for further study.
We chose Access because it was easier to understand than other large databases, and its license was included in Microsoft Office, making it easier to use. As we continued to study Access, our Access development skills improved over a relatively short period of time, and we prepared an Access prototype in parallel to clearly communicate our requirements along with the requirements definition document.
Next, we turned to in-house development and started with the definition of requirements. Based on the requirements definition, we tried to order a system vendor to create a program for us. The tool we were aiming for needed to incorporate the structure of electrical design and project execution that we had developed. There was a lot of tacit knowledge, and it was difficult to review and finalize the specifications. We were also concerned that the system vendor, who had no design knowledge, would not be able to accurately understand our intentions based on the requirements definition we had prepared. We decided to use a stand-alone design tool that we had created in Access about 20 years ago as a basis for further study.
We chose Access because it was easier to understand than other large databases, and its license was included in Microsoft Office, making it easier to use. As we continued to study Access, our Access development skills improved over a relatively short period of time, and we prepared an Access prototype in parallel to clearly communicate our requirements along with the requirements definition document.
Upsizing with AZD for cost-effective SQL development
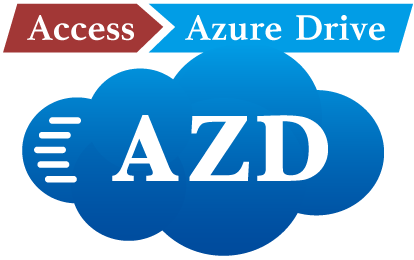
The Access prototype reflected our design requirements better than we had originally anticipated, but it was a stand-alone system that needed to be converted to a scalable tool that could be used in different countries. We approached several system vendors with the prototype of Access and requirements for an order, but the cost was not in line with our budget, and we might have had to limit the scope of development for the time being. In September 2022, while continuing to develop the prototype Access system while looking for opportunities to scale up, we received an email from Inforce. The email was an invitation to a seminar on the introduction of AZD, "Introducing a New Approach to Migrate Access to the Cloud (Migration to Azure SQL Database)" (*Watch the seminar video for free). We attended the seminar with high expectations that this might be a solution to our current problems, and we immediately asked Inforce to cloud-enable Access using AZD. The development was done by Inforce and tested by us, and with advice on modifications to Access that were necessary for the SQL conversion, the development proceeded smoothly and was completed on time.
Plans to use at locations around the world
Currently, we are preparing with our brunches in India and Indonesia to apply the developed SQL Server to the actual project. In parallel, we are also continuing to develop functional enhancements to Access, and the version has already improved significantly from the time we asked for development. We would like to ask for upsizing for the next version.
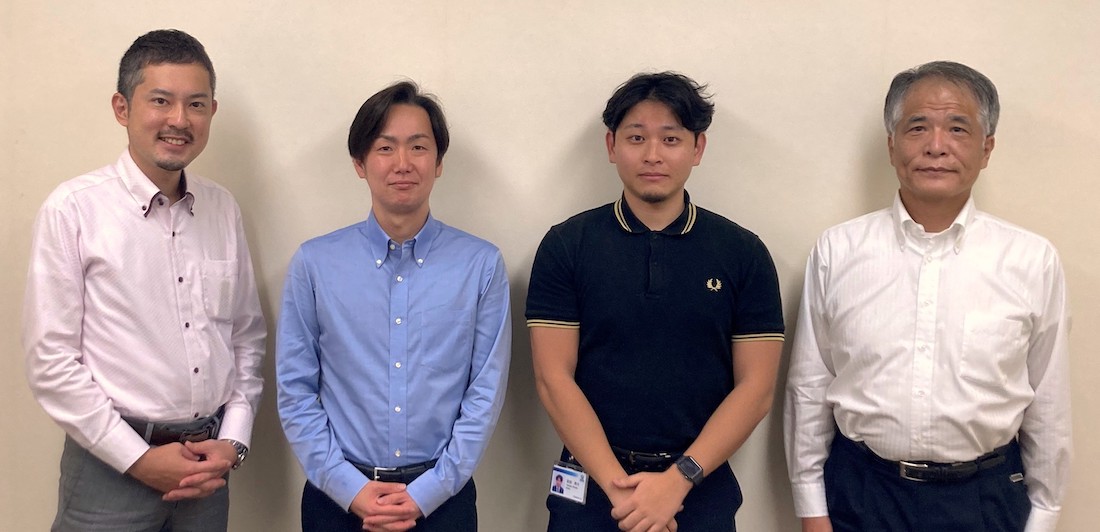